Water, air, and renewable energy are the sole resources for future H2O2 production, utilizing a novel electrolyser and concentrator technology
In Power2Hype, our goal is to replace the energy- and resource-intensive anthraquinone process for hydrogen peroxide production with an environmentally friendly electrolysis process. This innovative approach requires only water, air and green electricity to produce this chemical. The key lies in a new tandem electrolysis, which maximizes electricity usage, along with an innovative electrolyser and concentrator technology.
In work package 4, the partners DiaCCon (DIA), Fraunhofer IGB (Fh-IGB), Technicas Reunidas (TR) and SolvGe (Sol) collaborate on the design and construction of the electrolyser and the subsequent concentrator unit. Their focus extends to the integration into a cohesive overall system.
The development of electrolyzers kicks off with small scale lab cells (approx. 100 cm2), a step up from the current cells used in WP3. This initial phase defines the cell configuration, assesses component stability and test different process setups. Novel materials as electrodes and membranes supplied by WP2 will be integrated in the tailored-made cell. Fh-IGB and TR will contribute with computer-aided simulations of heat, H2O2 concentrations and flow fields. Laboratorey tests in WP3 will validate simulation results. Using insights from lab-scale electrolysers, a pilot electrolyser (approx. 400 cm2) will be designed and built for integration in the demonstrator developed in WP5.
Meanwhile, Sol focuses on downstream processing, developing a continuous H2O2 concentrator device, aiming concentrations of 70% pure H2O2 and above with high energy efficiency. The concentrator device, will also be integrated to the demonstrator in WP6.
Fh-IGB will actively contribute to the development of the components, aligning with an adaptative process development to meet specified target parameters. This involves a thorough exploration of various gas and fluid flows, along with operational parameters for paired electrolysis. The outcome, including process layout and mass flow diagram, serves as the foundation for the piloting the process in WP5.
WP4 bridges the scientific laboratory results (WP2 and WP3) and the plant construction (WP5). We are creating new component and processes to turn laboratory findings into real application.
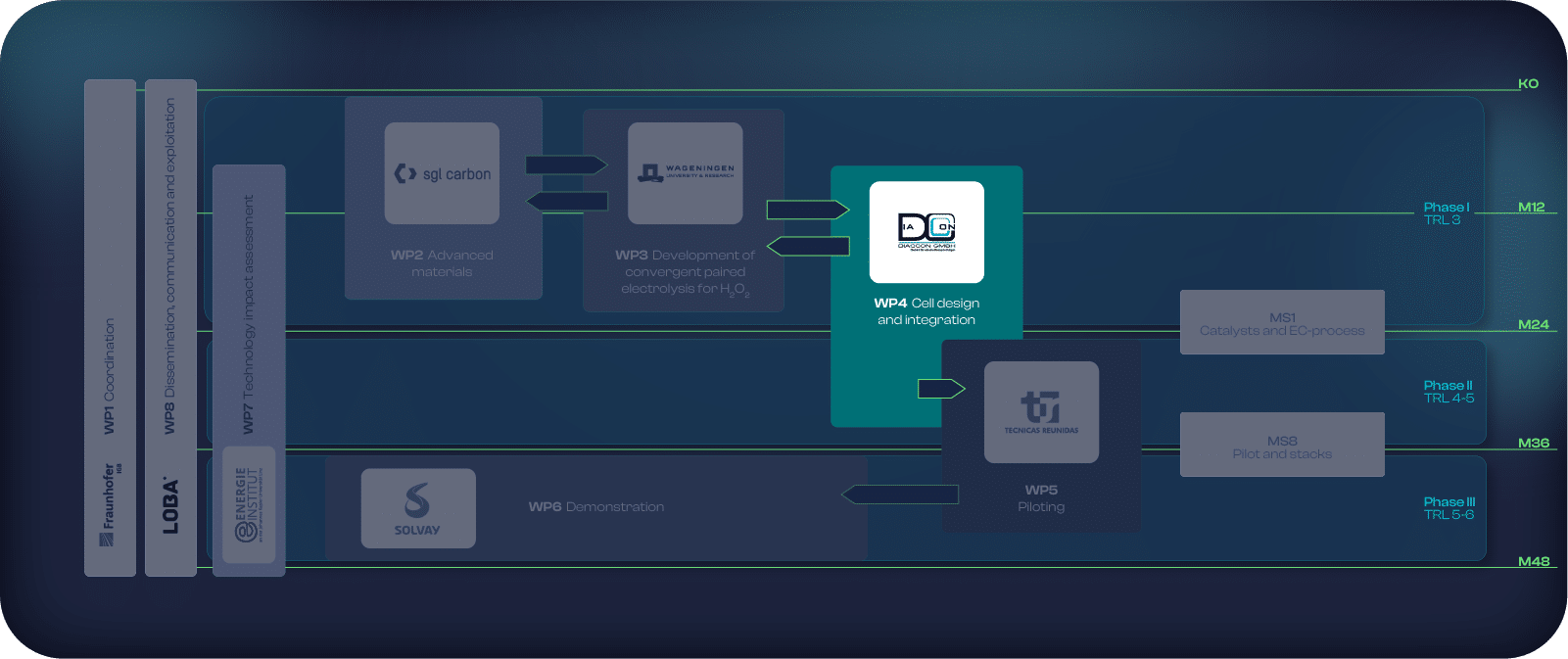